
• Argentina
Factories recovered by workers
Recovery of factories in practice 2
The economic dimension
Fixed assets and current assets form the firm.
Fixed assets determine the installed capacity and they include:
• Tangible assets
• Payable expenses or deferred intangible expenses, constituted by: studies and research; establishment and organization of the firm; administration costs and engineering during the installation period; licenses and patents; start-up costs; infrastructure realized outside of the firm and others;
• VAT of all expenses related to what was pais as tax. This remains as a fiscal credit in favor of the firm.
The current assets determine the level of exploitation of the installed capacity:
• Minimum availability of cash in loco and at the bank;
• Sale credits (the sale price shall include the utilities and the depreciation)
• Inventories: average stock of raw material; average stock of material; current and semi processed goods ( the proportion of depreciation has to be subtracted to general production costs); VAT is calculated exclusively on exchangeable goods and it remains fiscal credit for the firm to benefit.
The cost of finished goods sold by a firm is given by the box
Costs of finished goods
An investor can invest capital to recover a firm. But the objective of the investor is to maximize the returns of the investment. Both the return of the investment and the level of certainty of this return have to be sufficiently attractive for an investor to take the decision to invest amongst other investment options offered by the market.
The experience of the factories recovered by the workers overcame the cultural barrier related to the need of a working capital for the start up. The box shows how the operative strategy of the factories recovered by the workers allows the minimization of the needed capital.
Furthermore the investment in fixed assets is depreciated and they is distributed in the total sale cost within the production, administration, and commercialization costs. Final sales minus the total cost is to the economic utility.
Total cost
Raw Material |
In the beginning the decoupling point is in the supplier that minimizes the immobilization of the resources necessary for work |
Direct Labor (including social burden) |
This cost is replaced by applying utility |
Manifactiuring costs |
|
Depreciation |
This item is replaced by applying the utility to technical reserves |
Indirect personnel |
This item disappears since there is no supervision, and the maintenance goes directly under the direct labor cost |
Materials |
This application is necessary according to the characteristics of the process |
Energy and fuel |
Energy is a deferred cost, the application of labor over fuel depends on the process |
Taxes |
Its payment is deferred |
Insurance |
|
Rent |
|
Outsourcing |
|
Other |
|
Production expenses |
|
Start-up costs |
They are minimized by the experience of the workers |
Increase in the Stock of semi processed and processed goods |
|
Production costs |
|
Costs of production of what has been sold |
|
Administration costs |
|
Commercialization costs |
|
Financing costs |
|
Costs of what has been sold |
|
Sales provide cash and banks with an amount equivalent to the economic utility plus the total sale cost. Cash and banks increase in economic utility and a proportion of depreciation subtracted or added to the transfer of liquid assets to tangible assets ( exchange goods) or vice versa.
The total sale costs and the gross economic utility are accumulated in the sheets of the results throughout the period in analysis
From this gross utility we have to deduct the distribution among partners of the cooperative. In case it were a traditional firm the following applications would be deducted: taxes to revenues, management fees, and dividends.
Financial Dimension
The possibility to push a company to debt allows the investor to improve the rate of return in his investment. These debts have been one of the main factors for bankruptcy, when there is no chance of increasing financial costs or decreasing sales before an elevated breakeven point.
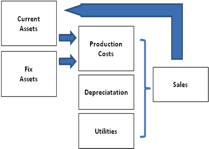
As above mentioned, this new productive model doesn’t require an investment in financial capital, since the input comes from the workers investing their human capital. It is the only resource available when credit or subsidies are lacking. In this way the workers are not just one more input for the firm as they are in the typical capital-managed firm, which applies costs of labor. Since the organization is horizontal the costs of indirect labor and the costs of administration, commercial and financial management disappear. After the first two phases, the factories start accumulating tangible assets to take advantage of scale economies in production, of the learning curve on the response to customers and on the operational cost, and this allows the to increase their market. Nowadays, the necessary funds for starting new cooperatives (conformation of the cooperative, re-connection to public services, electricity, gas, water and telephone, maintenance of certain initial production lines) are generally provided by the cooperation of other recovered factories.

DOWNLOAD THE BROCHURE PDF
Spanish (0.5 MB)English (0.5 MB)
Italian (0.5 MB)

ONLY TEXT
•Recovery of factories in practice